NextStar Energy EV Battery Plant
Canada’s First Advanced EV Battery Manufacturing Facility Megaproject
NextStar Energy, a CA$5 billion megaproject in Windsor, Ontario, sponsored by joint venture between Stellantis and LG Energy Solution, is set to become Canada’s first large-scale electric vehicle (EV) battery production plant.
NextStar is the largest investment in Canadian automotive history. With a projected annual capacity of 49.5 GWh, enough to power 450,000 EVs. This facility represents a major shift in the Canada’s approach to sustainable transportation and it marks an important milestone in the transition toward cleaner mobility (1).
The global move toward electric vehicles is reshaping industries and economies, and at the heart of this transition lies battery technology. Windsor, Canada’s “automotive capital,” has faced its share of challenges over the years, from shifts in manufacturing to the impacts of economic downturns. Yet, through resilience and adaptability, the city is positioning itself at the forefront of the EV revolution (2).
The NextStar project is expected to create up to 2,500 jobs, offering new opportunities in advanced manufacturing and reinforcing Windsor’s role in the evolving automotive landscape. More than just an economic boost, this initiative reflects a broader commitment to innovation and sustainability in Canadian industry.
This article explores the several dimensions of the NextStar project:
Project Highlights, Timeline, and Team
Financing Structure
Risks and Complexities
Lithium-Ion Pouch Type Batteries
Project’s Social Impacts
Sustainable Development
Windsor’s Automotive Legacy
Project Highlights, Timeline, and Team
The NextStar Energy facility spans up to 4.5 million square feet on a 220-acre site. At its core, the facility consists of two primary structures:
Cell Building (2.7 million SF): Dedicated to manufacturing lithium-ion battery cells, ensuring high-capacity energy storage for EVs.
Module Building (445,000 SF): Responsible for assembling battery cells into modules, completing the final product before distribution.
The supporting infrastructure includes a master substation, an electrolyte supply system, safety and waste management units, and solvent recovery systems—all designed to enhance efficiency, safety, and sustainability in battery production.
The main production facilities feature high-precision cleanroom and dry room environments to maintain strict humidity and temperature controls, alongside integrated module assembly lines that ensure efficient production and quality assurance.
The project was reported to include at least 38,000 tons of structural steel supplied, along with 3,100 tons of steel joists and 420,000 square feet of decking. The mechanical, HVAC, and utility systems are equally extensive, including 5 million pounds of sheet metal for ventilation and air control, more than 75 miles of hydronic and plumbing pipes, and over 900 HVAC units to maintain precise climate conditions essential for battery production.
Project Timeline
The project was reported to have reached approximately 30% completion by December 2023, with the Module Building fully enclosed and structural steel installation completed. At that time, equipment installation had begun, while the Cell Building was nearing completion of its structural framework, with around 40% of its exterior enclosed (4).
The first phase of operations, focusing on battery module production, was reported to be on track for launch in the first half of 2024. Cell manufacturing, a critical component of the facility’s output, was projected to begin in 2025, with full production expected by 2026 (5).
NextStar reported to have officially commenced battery module production in October 2024, marking a milestone in the project’s transition from construction to operation. The project has also been making strides in workforce development, with over 450 of the projected 2,500 jobs reportedly filled (6).
Project Team
The execution relied on a diverse network of stakeholders, including industry leaders, contractors, engineers, and suppliers. At its core, NextStar Energy, a joint venture between Stellantis and LG Energy Solution drives the plant’s development and oversees its construction and operations.
Sponsors:
Stellantis: Global automaker and co-founder of NextStar Energy, responsible for overseeing battery production and integration into its EV supply chain(7).
LG Energy Solution: Leading battery manufacturer, co-founder of NextStar Energy, bringing expertise in lithium-ion battery production (8).
NextStar Energy: The joint venture entity responsible for the construction, management, and operation of the Windsor EV battery plant (3).
Contractors, Engineers, and Suppliers:
Alberici-Barton Malow (A-BM): A joint venture comprised of Alberici and Barton Malow is the Design-builder responsible for the construction of the 4-million-square-foot facility, including preconstruction, steel fabrication, and concrete work (9).
Kasian Architecture Interior Design and Planning Ltd.: Architect of record for the Module Building, responsible for architectural design in collaboration with Gresham Smith, Stantec (Formerly Morrison Hershfield), and A-BM (10).
Gresham Smith: Architecture firm collaborating on the Module Building design for NextStar Energy. Structural Engineers (11).
Stantec (Formerly Morrison Hershfield): Engineering firm involved in various aspects of the facility’s development. (12).
SMRT Architects and Engineers: Providing cleanroom and dry room envelope design and engineering services in collaboration with Hodess Cleanroom Construction (13).
Hodess Cleanroom Construction: Specializing in cleanroom construction for battery manufacturing processes (13,14).
Black & McDonald: Responsible for mechanical and HVAC systems, including installing 5 million pounds of sheet metal, 75+ miles of hydronic and plumbing pipe, and 900 HVAC units (15).
Walters Group: Tasked with installing 3,100 tons of steel, joists, and 420,000 square feet of decking within a four-month timeframe (16).
Hillsdale Fabricators: A division of Alberici, supplying 38,000 tons of structural steel for the facility (9,17).
Financing Structure
NextStar Energy reflects a strategic collaboration between industry and government, aligning private investment with public incentives.
At the core of the funding structure is a public-private partnership, where government contributions are tied to production milestones. Stellantis is investing CA$3.4 billion in plant construction, while the federal and Ontario governments have each pledged CA$500 million toward development costs. However, much of the government subsidies are conditional on the facility meeting specific production targets, ensuring that public funding is linked to tangible economic and environmental returns (18).
Based on LG Energy Solution's financial statements as of June 30, 2024, the company has committed to investing US$1.464 billion in the joint venture with Stellantis and has already contributed US$765 million. The agreement includes a clause that allows either party to purchase the other's shares in the event of a default, ensuring mutual commitment to the project's success (8).
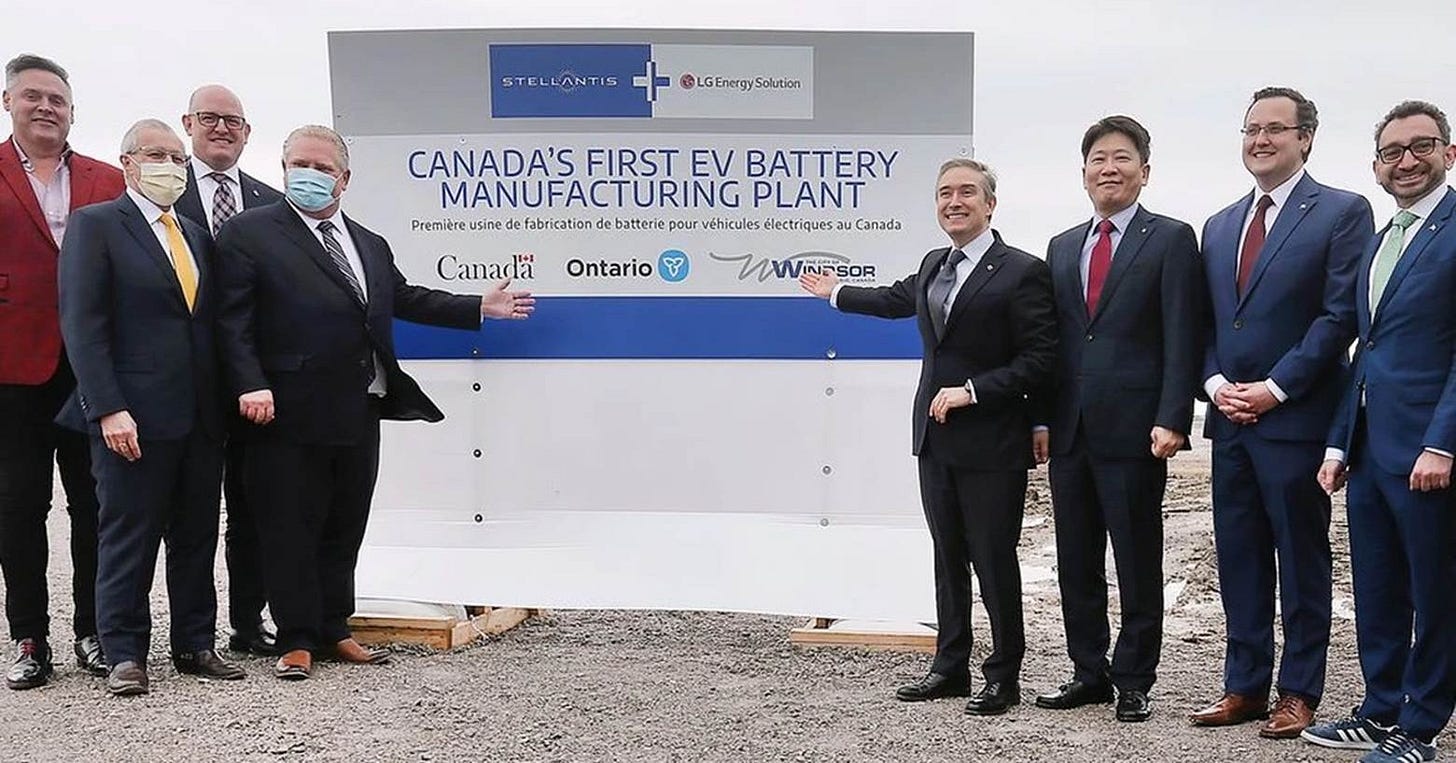
Risks and Complexities
Project Completion and Ramp Up
Executing a project of this scale comes with a unique set of challenges, requiring advanced design strategies, global coordination, and sophisticated logistics to ensure smooth construction and production.
Innovative Design and Construction: To meet the project's ambitious timeline, prefabrication and digital project management tools have played a crucial role in optimizing efficiency. One of the project stakeholders highlighted the use of Navis, Revit, BIM 360, Procore, Blue Beam, and P6 in their workflow (15). By prioritizing off-site prefabrication, the project has been able to reduce onsite labor demands and accelerate field installation, a crucial factor in meeting the tight construction schedule.
Global Coordination: Given the number of architecture firms, consultants, and stakeholders involved—many spreads across multiple countries—seamless communication and precise coordination are critical to maintaining progress. As the facility ramps up operations, NextStar Energy is collaborating with LG’s facilities in Poland to supply interim battery cells, ensuring production continuity while local manufacturing scales up.
Sophisticated Logistics and Manufacturing Risks: The facility is designed with advanced logistical systems to optimize the movement of raw materials and finished battery cells. However, manufacturing EV batteries at scale presents stringent quality control challenges.
Supply Chain Vulnerabilities
The EV battery supply chain is highly complex and geographically concentrated, making it susceptible to disruptions.
A significant portion of battery-grade materials and components are processed in a limited number of countries, notably China, which controls a substantial share of the global battery supply chain.
In early 2025, the Trump administration proposed a 25% tariff on imports from Canada and Mexico, including automotive parts and metals essential for EV manufacturing (19). This policy aimed to encourage domestic production but introduced challenges for the North American EV industry, which relies on a seamless cross-border supply chain. The tariffs will lead to increased production costs, potential delays, and uncertainty within the industry.
Automakers and suppliers are now reassessing their supply chain strategies, considering relocating production to the U.S. or other regions to mitigate the impact of these tariffs. The lack of regulatory stability is a major risk to continued economic success and thriving of EV battery projects in north America.
Economic and Financial Challenges
The financial viability of EV battery plants is influenced by fluctuating demand for electric vehicles, high production costs, and intense global competition.
The collapse of major European EV battery producer Northvolt in November 2024 underscores the financial risks inherent in the industry, where even well-funded companies can face insolvency due to production challenges and market dynamics (20).
Technology Obsolescence
The rapid evolution of battery technology presents a fundamental challenge for EV battery plants, where large-scale investments in current production methods may risk becoming obsolete as new, more efficient, and cost-effective solutions emerge.
Innovations such as solid-state batteries and lithium-sulfur chemistries are being actively explored to enhance energy density and reduce reliance on scarce raw materials. Companies like Lyten are making significant strides in lithium-sulfur battery production, aiming to disrupt traditional supply chains and improve performance. However, while these next-generation technologies hold promise, they also face hurdles, including technical barriers, high development costs, and the need for new manufacturing processes—all of which could affect the long-term viability of existing battery production facilities (21).
CEO Danies Lee recently emphasized the NextStar Energy plant’s flexibility within lithium-ion technology, highlighting LG Energy Solution’s track record in navigating advancements in battery chemistry over the past two decades. “We’re pretty flexible under the umbrella of lithium-ion battery technology,” Lee noted. “When it comes to the lithium process and chemistry, we can respond to change” (5).
The Windsor plant has been designed with adaptability in mind, allowing for simultaneous production of different battery types while ensuring that its cells remain versatile across multiple vehicle platforms. This strategic approach reflects an industry-wide recognition that resilience and innovation must go hand in hand—balancing the demands of today’s market with the breakthroughs of tomorrow (5).
Lithium-Ion Pouch Type Batteries
NextStar Energy’s decision to manufacture pouch-type lithium-ion batteries marks a shift in the electric vehicle (EV) battery sector, leveraging their unique advantages in space efficiency, energy density, and safety (22).
Unlike traditional cylindrical or prismatic lithium-ion batteries, pouch batteries utilize a flexible aluminum foil casing rather than a rigid metal enclosure, allowing for customizable shapes that optimize space within EV battery packs. This design enhances energy efficiency and reduces weight, a crucial factor for improving EV range.
The manufacturing process, although complex, includes a cutting-edge “degassing” method developed by LG Energy Solution, which improves efficiency and reduces the common issue of electrolyte leakage. In 2022, pouch-type batteries accounted for 26% of the market share in the EV battery industry and are projected to increase to 31% by 2030 due to their high energy density and flexible applications (23).
Unlike lithium-sulfur (Li-S) batteries, which utilize sulfur-based cathodes for higher energy density but suffer from a shorter cycle life, pouch-type batteries rely on conventional lithium-ion chemistry with a liquid electrolyte.
Additionally, all-solid-state batteries, a next-generation alternative, replace the liquid electrolyte with a solid electrolyte, enhancing safety by eliminating leakage risks and improving longevity. While pouch-type batteries still contain liquid electrolytes and require advanced safety measures, their design flexibility, high energy density, and thermal efficiency make them a preferred choice for next-generation EVs, supporting the industry's shift toward lighter, more efficient, and sustainable energy storage solutions (23).
Manufacturing of Lithium-Ion batteries
Lithium-ion batteries generate electricity by moving lithium ions between the cathode and anode during charging and discharging.
The cathode determines capacity and voltage, while the anode, typically graphite, influences lifespan due to structural wear over cycles.
Research into silicon anodes aims to improve capacity and efficiency. The electrolyte, available in liquid, solid, or gel forms, enables ion transport and must maintain high conductivity and stability. A separator, usually made of polyethylene or polypropylene, prevents direct contact between the cathode and anode while allowing ion flow and shutting down at high temperatures. Efforts to develop thinner separators seek to enhance energy density and reduce battery size. Manufacturing process of Lithium-Ion batteries entails four main steps:
Electrode Manufacturing: Mixing, coating, and rolling cathode and anode materials with binders and solvents to enhance adhesion and conductivity. The coated materials are then compressed into electrodes.
Cell Assembly: Integrating separators and electrolytes with electrodes, assembling them into mono-cells or bi-cells using stacking or winding techniques.
Formation Process: Charging and discharging cells to stabilize performance, followed by aging and degassing to remove trapped gases.
Pack Process: Configuring assembled cells into battery packs, connecting multiple cells, and enclosing them in protective casings for final use.
Project’s Social Impacts
The economic impact of NextStar Energy extends beyond its initial capital investment, serving as a catalyst for broader industrial transformation in Canada’s automotive sector.
As the Canada’s first large-scale EV battery plant, the project is shaping regional supply chains, workforce development, and economic resilience in ways that will endure long after its construction.
Job Creation and Workforce Development: With over 7,500 tradespeople engaged in its construction and 2,500 permanent manufacturing roles, NextStar Energy is a major employment driver. Workforce development programs, such as the Battery Boost initiative, are helping to train local talent, ensuring a steady pipeline of skilled workers for Canada’s growing EV industry (1). At its peak, the project is expected to involve 3,200 tradespeople and equipment installers, with 2,300 of those positions filled by Canadian workers (4).
Strengthening North America’s Supply Chains: Strategically located in Windsor—Canada’s automotive capital—the plant enhances supply chain efficiency by reducing dependence on imported materials. This integration strengthens North America’s EV ecosystem, making the region less vulnerable to external disruptions and creating a more resilient production network.
Attracting Ancillary Industries and Investment: The presence of a gigafactory of this scale is expected to attract key supporting industries, including raw material suppliers, logistics providers, and technology firms. This multiplier effect extends economic benefits beyond automotive manufacturing, reinforcing Windsor’s role as a critical node in the future of clean transportation.
The project has not been without controversy. The employment of 900 South Korean workers has drawn criticism from Canadian labor unions, who argue that domestic tradespeople are qualified for these roles. In response, NextStar Energy has defended the decision, stating that these workers are temporary specialists hired by external suppliers for highly technical installations essential to the plant’s operations (18).
Sustainable Development
EV Battery plants align with key United Nations Sustainable Development Goals (SDGs), integrating sustainability principles into its operations and setting a precedent for responsible industrial growth.
EV Battery plants affect the following four SDGs directly.
SDG 7 - Affordable and Clean Energy: By manufacturing batteries for EVs, the facility directly contributes to reducing greenhouse gas emissions and transitioning to renewable energy sources.
SDG 8 - Decent Work and Economic Growth: The project is expected to generate 2,500 jobs in manufacturing alone, alongside numerous indirect opportunities in construction, logistics, and supply chain management (24).
SDG 13 - Climate Action: The adoption of low-carbon energy solutions in battery production is aligned with Canada’s net-zero commitments.
SDG 12 - Responsible Consumption and Production: The integration of recycling processes ensures that raw materials are recovered and reused, minimizing environmental harm.
NextStar Energy is aiming to prove that economic growth and environmental responsibility can go hand in hand.
Windsor’s Automotive Legacy
Windsor’s emergence as an EV hub is the product of strategic planning, economic incentives, and cross-sector collaboration. Community Improvement Plans (CIPs) have played a key role, attracting private investment through financial incentives like property tax exemptions. The Brownfield Redevelopment CIP, for example, has delivered a 13:1 return on investment, underscoring the impact of public-sector incentives in driving economic growth.
After years of economic decline, Windsor is rebounding. Population growth (3% between 2011–2016) and a steady drop in unemployment signal recovery, while GDP growth, particularly in 2014–2015, marked a turning point. However, Windsor’s economy still lags slightly behind the national average.
Collaboration has been central to this revival. Invest WindsorEssex, local universities, and government agencies have worked to attract investment, develop training programs, and build specialized facilities like a state-of-the-art battery testing lab. Government support at all levels has anchored large-scale projects shaping Windsor’s industrial future.
Resilience has long defined Windsor’s automotive sector. From its early days as the "Border Cities" growing alongside Detroit, it has weathered downturns, bailouts, and trade shifts. The 1965 Auto Pact once secured investment in Canadian factories, but globalization, trade liberalization, and rising competition have eroded those advantages.
The NextStar battery plant is now at the center of Windsor’s economic reinvention. More than a manufacturing site, it’s a research and development hub for vehicle electrification, attracting further investment and solidifying Windsor’s role in advanced automotive technology.
Question then Becomes
The NextStar Energy project represents a landmark investment in Canada’s EV future, bringing together industrial ambition, government backing, and strategic foresight. Yet, the project exists at the intersection of technological change, policy shifts, and global competition—factors that will shape its trajectory in the years to come.
Nestled in Windsor, a city uniquely positioned to weather both supply chain vulnerabilities and regulatory headwinds, NextStar Energy appears well-placed to navigate the turbulence of the EV battery market. Yet, is this strategic positioning enough to secure the project’s economic success?
With the Trump administration proposing a 25% tariff on Canadian automotive components, the question then becomes: how will shifting trade policies and geopolitical uncertainties reshape the financial calculus of NextStar and similar EV battery ventures? Will the project’s economic foundation hold firm?
Notes
Join the EPM Network to access insights, influence our research, and connect with a community shaping the industry's future.
Support us by sharing this article with your friends and colleagues.
If you wish to share your opinion, provide insights, or correct any details in this article, please email editor@epmresearch.com.
Refer to this article using the following citation format:
Zangeneh, P., Abbasi M. (2025), “NextStar Energy EV Battery Plant: Canada’s First Advanced EV Battery Manufacturing Facility Megaproject” EPM Research Letters.
References
Yakub M. Electric Autonomy Canada. 2024. NextStar Energy begins battery module production in Windsor. Available from: https://electricautonomy.ca/ev-supply-chain/2024-10-23/nextstar-battery-windsor-production-canada/
Taylor I. Turnaround Cities: Anglo-Saxon Case Studies Insights from Pittsburgh (PA), Newcastle (NSW) and Windsor (Ont.).
Nextstar Energy. Official Website.
New NextStar Energy EV Battery Plant Celebrates ‘Topping Out’ Ceremony as Construction reaches 30 Per cent Completion. Stellantis Blog.
Windsorstar 2024. Windsor NextStar’s parent company reveals battery future plans.
Stellantis Media. NextStar Energy Announces Start of Battery Module Production.
Stellantis.com. Official Website.
LG Energy Solution. Official Website.
Alberici. NextStar Energy EV Battery Plant. Offical Website.
Kasian. EV Battery Plant: Powering Progress - Designing the Future of EV Batteries. Official Website.
Gresham Smith. Official Website.
Stantec to acquire Morrison Hershfield, a leading transportation, buildings, and environmental services firm. Press Release.
SMRT. NextStar Energy Electric Vehicle Battery Plant. Official Website.
Hodess Cleanrooms. Official Website.
Black & McDonald. Stellantis: Revolutionizing the North American EV Industry. Official Website.
Walters Group Inc. NextStar Energy EV Battery Plant. Official Website.
Alberici Hillsdale. Automotive | Hillsdale | Structural Steel Fabrication. Official Website.
Global News. Foreign workers at subsidized EV battery plant a ‘slap in the face’: union. Globalnews.ca.
CES Trump’s tariff threat spurs auto suppliers to rethink production plans. Reuters.
Mannes M. Exclusive: Scania tries to breathe life into troubled EV battery maker Northvolt. Reuters
Chu A, Smyth J, Temple-West P. $1bn US battery plant plan shows race to reduce reliance on China. Financial Times.
NextStar Energy Announcement on Pouch Batteries. LinkedIn Post.
LG Energy Solutions. ENSOLPEDIA | BATTERY INSIDE.
Automotive Logistics. Stellantis and LG Energy Solution begin battery production in Canada. Automotive Logistics.